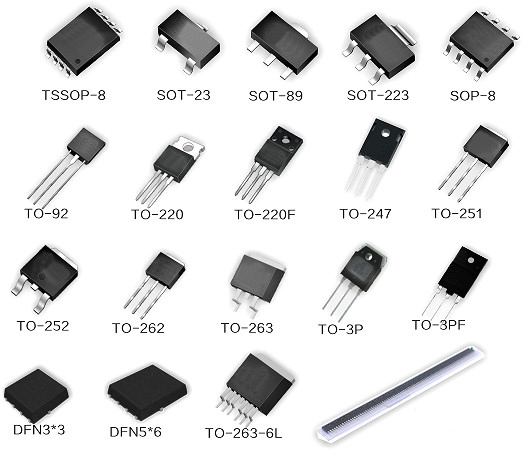
在電機驅(qū)動和電源轉(zhuǎn)換場景中,MDDMOS管的嚴重發(fā)熱是工程師們經(jīng)常面臨的挑戰(zhàn)。某工業(yè)伺服驅(qū)動器因MOS管溫升高達105℃,導致系統(tǒng)頻繁觸發(fā)過溫保護。本文將深入分析發(fā)熱機理,并結(jié)合實測數(shù)據(jù),提供從散熱設計到驅(qū)動優(yōu)化的系統(tǒng)性解決方案。
一、發(fā)熱根源:損耗模型的精準拆解
MOS管發(fā)熱的根本原因是能量損耗的累積,主要包括以下幾個方面:
導通損耗:其計算公式為P=IMsxRs(o)xD。以某50A電機驅(qū)動案例為例,當Rds(on)=5mΩ,占空比D=70%時,導通損耗可達8.75W。
開關損耗:其計算公式為P=號xVpsxIDx(t,+tf)xfsw。在100kHz開關頻率下,600V/30A工況的開關損耗可突破15W。
寄生導通損耗:米勒效應引發(fā)的寄生導通(Cgd耦合)在高壓場景下會額外產(chǎn)生3-5W的損耗。
二、散熱設計四步優(yōu)化法
以某1kW LED電源的MOS管(TO-220封裝)為例,其實測殼溫高達98℃。
封裝熱阻解析:熱阻鏈模型為Ti=Pdiss x(RoIC+ ROCS + RSA)+T。TO-220的典型熱阻值為RθJC=1.5℃/W,RθCS(導熱膏)≈0.5℃/W,RθSA(散熱器)=15℃/W,總熱阻為17℃/W。當功率損耗為15W時,溫升ΔT可達255℃,遠超安全限值。
散熱器升級方案:更換齒高15mm的鋁擠散熱器(RθSA=8℃/W),并添加0.5mm厚的相變導熱片(RθCS=0.2℃/W),新熱阻為9.7℃/W,溫升降至145.5℃。
PCB散熱增強:采用2oz厚銅箔,增加散熱過孔(孔徑0.3mm,間距1mm),并將銅箔面積擴展至15×15mm²,熱阻降低40%。
多管并聯(lián)均流:并聯(lián)3顆MOS管,單管電流降至1/3,導通損耗降為原值的1/9。
三、驅(qū)動波形優(yōu)化三大關鍵
以某光伏逆變器因驅(qū)動異常導致開關損耗占比超60%的案例為例。
驅(qū)動電阻精準匹配:根據(jù)Qg參數(shù)計算最優(yōu)Rg。當Qg=45nC、Ciss=3200pF時,Rg=4.7Ω(原設計22Ω)。實測結(jié)果表明,開關時間從82ns縮短至28ns,損耗降低65%。
米勒平臺震蕩抑制:增加RC緩沖電路(R=10Ω,C=1nF),米勒電荷Qgd吸收效率提升70%,振蕩幅度從4V降至0.8V。
負壓關斷技術:采用-3V關斷電壓,死區(qū)時間縮短至50ns,寄生導通概率從12%降至0.3%。
四、實測案例:伺服驅(qū)動器溫升優(yōu)化
初始狀態(tài):MOS管型號為IPB65R080CFD,工況為VDS=400V,ID=20A,fsw=20kHz,殼溫102℃,效率89%。
優(yōu)化措施:
散熱改造:替換為銅基板散熱器(RθSA=5℃/W),涂抹石墨烯導熱墊(熱導率15W/mK)。
驅(qū)動調(diào)整:將Rg從15Ω降至3.3Ω,增加門極負壓-5V,并聯(lián)Cgd=220pF加速米勒電荷泄放。
拓撲改進:增加ZVS輔助電路,實現(xiàn)軟開關。
優(yōu)化結(jié)果:殼溫降至61℃,效率提升至94%,開關損耗占比從58%降至22%。
五、未來技術:寬禁帶器件的熱管理革命
GaN器件優(yōu)勢:橫向結(jié)構(gòu)降低熱阻,如GaN Systems GS-065-011-1-L的熱阻僅1.2℃/W,零反向恢復特性消除Qrr損耗。
SiC MOS方案:3D封裝技術(如Wolfspeed WolfPACK™)使熱阻降低50%,高結(jié)溫耐受(Tj_max=175℃)。
通過散熱設計與驅(qū)動技術的協(xié)同優(yōu)化,MDDMOS管溫升可降低60%以上。隨著第三代半導體的普及,熱管理策略需同步革新,從被動散熱轉(zhuǎn)向動態(tài)熱調(diào)控,結(jié)合溫度傳感器與驅(qū)動IC實時調(diào)節(jié)開關參數(shù),實現(xiàn)智能溫控。
〈烜芯微/XXW〉專業(yè)制造二極管,三極管,MOS管,橋堆等,20年,工廠直銷省20%,上萬家電路電器生產(chǎn)企業(yè)選用,專業(yè)的工程師幫您穩(wěn)定好每一批產(chǎn)品,如果您有遇到什么需要幫助解決的,可以直接聯(lián)系下方的聯(lián)系號碼或加QQ/微信,由我們的銷售經(jīng)理給您精準的報價以及產(chǎn)品介紹
聯(lián)系號碼:18923864027(同微信)
QQ:709211280